In the realm of industrial systems, operating under high pressure is a common scenario. Ensuring the safety of both equipment and personnel in such environments is essential. This is where safety devices like rupture discs (also known as rupture disks) and burst discs (or burst disks) play a crucial role. These devices are among the most reliable and widely utilized in the industry to safeguard against potential hazards.
Rupture discs are designed to prevent catastrophic failures by relieving excess pressure in a controlled manner. They are essential components in systems such as pressure vessels, reactors, condensers, bio reactors, heat exchangers and pipelines. By releasing built-up pressure, these discs mitigate the risk of pressure rise and significant damage, thus protecting both machinery and human lives.
This comprehensive guide delves into the intricacies of rupture discs, exploring their various types, numerous applications, and the reasons why they are indispensable in modern industrial operations. From understanding their fundamental working principles to learning about their critical role in maintaining safety standards, this guide covers everything you need to know about rupture discs.
What is a Rupture Disc / Burst Discs ?
A non-reclosing pressure relief device engineered to burst at a predetermined pressure. This intentional burst action is crucial for safeguarding systems that operate under pressure, such as pressure vessels, air compressors, and pipelines. The primary function of a rupture disc is to prevent overpressure conditions, which can lead to catastrophic failures, equipment damage, and potential harm to personnel.
These devices are specifically designed to offer immediate pressure relief by rupturing when the internal pressure exceeds safe levels. Unlike other pressure relief devices, rupture discs do not reset or close after activation. Instead, they provide a single-use solution, full bore ensuring that excess pressure is promptly released, thereby maintaining the integrity and safety of the system.
Rupture discs are integral components in various industrial applications due to their reliability, precision, and rapid response capabilities. They are utilized in environments where consistent and dependable pressure management is vital, ensuring operational safety and efficiency. By incorporating rupture discs into pressure control systems, industries can effectively mitigate risks and enhance overall safety measures.

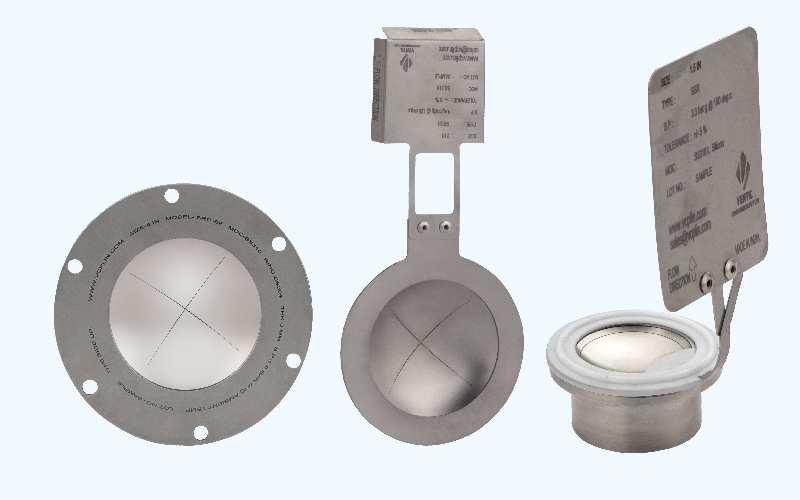
Key Features :
- Non-reclosing : Once the disc bursts, it cannot be reset.
- Non-mechanical : Unlike pressure relief valves, rupture discs have no moving parts.
- Pressure Relief : Designed to relieve excess pressure quickly and effectively.
- High Reliability : Provides failsafe performance with minimal maintenance.
- Cost-Effective : Economical compared to other safety devices.
- Leak-Tight : Ensures no leakage prior to activation.
- Wide Applications : Used in chemical processing, oil and gas, pharmaceuticals, and more.
- Quick Response : Reacts swiftly to pressure changes.
- Safety : Protects both equipment and personnel from potential hazards
Types of Rupture Discs
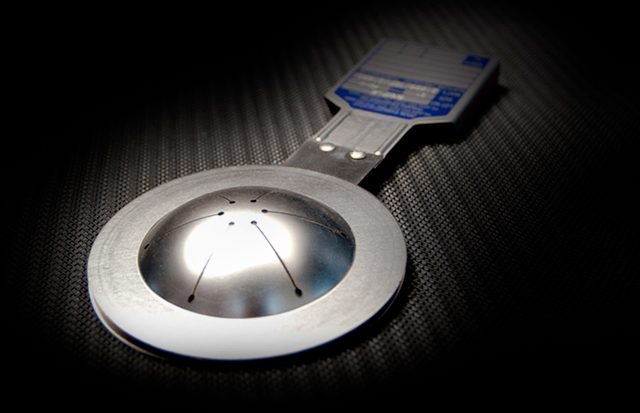
1. Forward Acting Rupture Discs
Designed with the dome facing the process side, these are suitable for high-pressure systems and offer a simple, cost-effective solution.
- Design : The dome is oriented toward the process side (pressure is applied to the convex side).
- Applications : Suitable for static or high-pressure systems.
- Advantages : High-pressure tolerance, cost-effective, and simple design.

2. Reverse Acting Rupture Discs
Feature an inverted dome that bursts at a defined pressure, ideal for low-pressure or high-cycle applications with better fatigue resistance.
- Design : The dome is inverted toward the pressure source (pressure is applied to the concave side).
- Applications : Ideal for low-pressure applications or where frequent cycling occurs.
- Advantages : Increased fatigue resistance, Can handle operating pressures closer to the burst pressure, Allows use of complex sensing mechanisms.
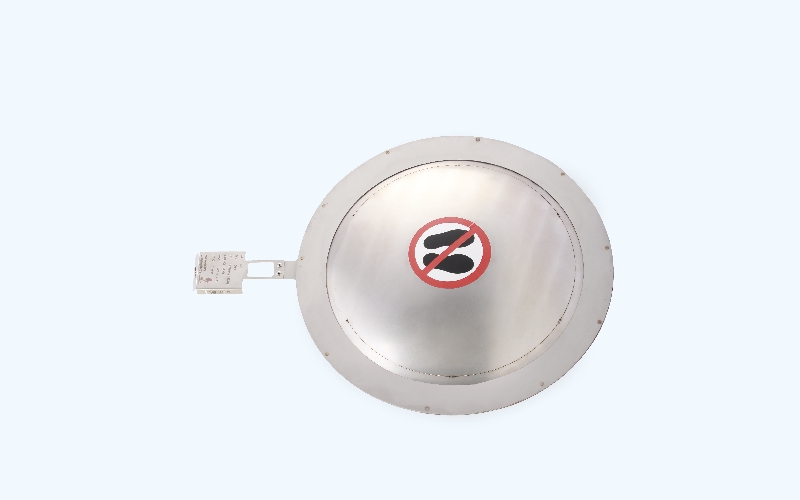
3. Composite Rupture Discs
Constructed with multiple layers, these are highly customizable and resistant to corrosive or extreme temperature environments.
- Design : Made of multiple layers of materials, with a sealing layer often combined with a metal or non-metallic bursting layer.
- Applications : Used in systems with corrosive media or variable temperature environments.
- Advantages : Highly customizable for specific applications and resistant to corrosion or chemical attack.
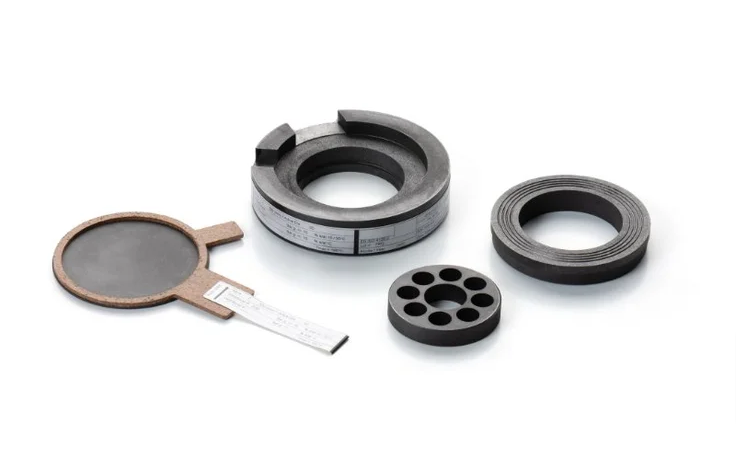
4. Graphite Rupture Discs
Made from graphite, they excel in highly corrosive settings with excellent chemical resistance and non-sparking properties.
- Design : Constructed from graphite, often with a protective coating.
- Applications : Ideal for highly corrosive environments.
- Advantages : Excellent corrosion resistance and non-sparking properties.
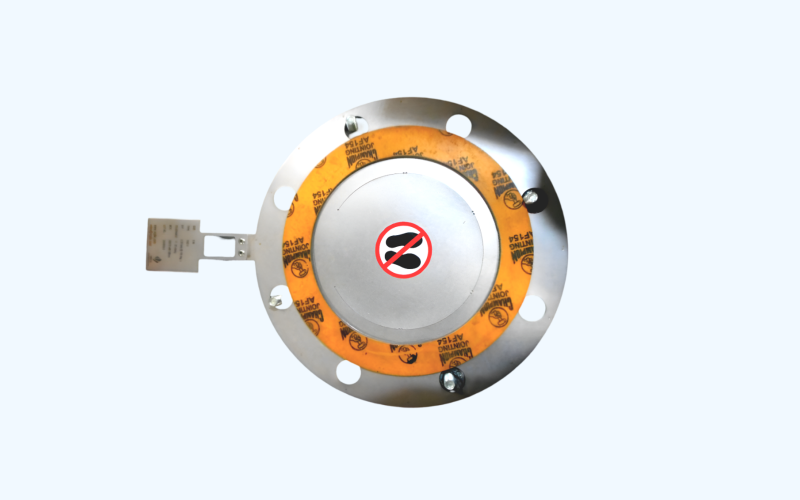
5. Vacuum-Support Rupture Discs
Equipped with support structures to prevent collapse under vacuum conditions, suitable for processes experiencing backpressure.
- Design : Include a support structure to prevent the disc from collapsing under vacuum conditions.
- Applications : Used in processes subject to vacuum or backpressure conditions.
- Advantages : Ensures functionality in vacuum environments.
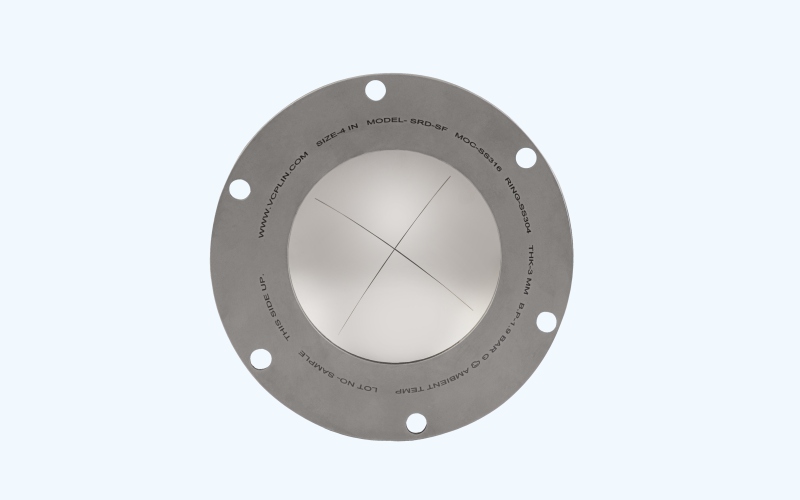
6. Scored Rupture Discs
Pre-scored to control rupture patterns, they minimize fragmentation and provide precise and predictable bursting.
- Design : The disc is pre-scored to control the rupture pattern.
- Applications : Used where predictable opening patterns are essential.
- Advantages : Minimizes fragmentation and ensures precise burst control.
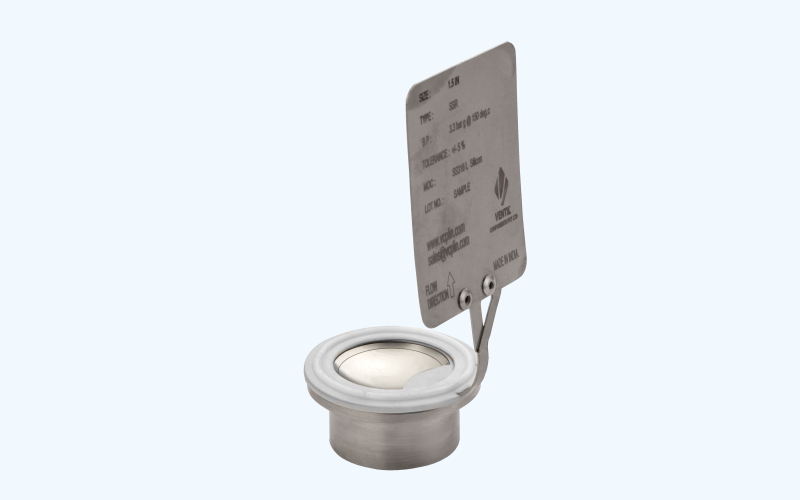
7. Sanitary Rupture Discs
Polished and hygienic designs for pharmaceutical, food, and beverage industries, compatible with CIP/SIP systems.
- Design : Meet stringent hygiene requirements, with polished surfaces and crevice-free designs.
- Applications : Used in pharmaceutical, food, and beverage industries.
- Advantages : Compatible with Clean-in-Place (CIP) and Sterilize-in-Place (SIP) systems.
8. High-Temperature Rupture Discs
Built with temperature-resistant materials, they perform reliably under extreme thermal conditions in industries like aerospace or petrochemicals.
- Design : Built with materials resistant to extreme temperatures, such as Inconel or Hastelloy.
- Applications : High-temperature processes, such as petrochemical or aerospace industries.
- Advantages : Reliable performance under extreme thermal conditions.
Applications of Rupture Discs :
Rupture discs are vital safety devices across various industries, ensuring operational safety and efficiency. Below are some common applications:
- Pressure Vessels : Rupture discs act as a critical safety mechanism in pressure vessels, releasing excess pressure to prevent equipment failure. They are often used alongside pressure release valves to enhance system safety.
- Air Compressors : In air compressors, bursting discs prevent overpressure scenarios that can damage the system or lead to hazardous situations. These discs ensure seamless operation under varying pressures.
- Steam Systems : Rupture discs are frequently integrated with steam traps to regulate and release pressure in steam boilers and pipelines. Steam trap manufacturers in India often recommend rupture discs as an additional safety measure.
- Chemical Processing : Corrosive environments in the chemical industry require specialized rupture disk types like graphite discs to handle extreme conditions effectively.
- Storage Tanks and Pipelines : Rupture discs are used in storage tanks and pipelines to prevent overpressure due to thermal expansion or sudden pressure surges.
Rupture Discs: Working Principle
The rupture disk working principle is straightforward: when the system pressure exceeds the disc’s rated capacity, it ruptures instantly, releasing pressure and safeguarding the equipment. Unlike a pressure release valve, a rupture disc is a one-time-use device and must be replaced after activation.
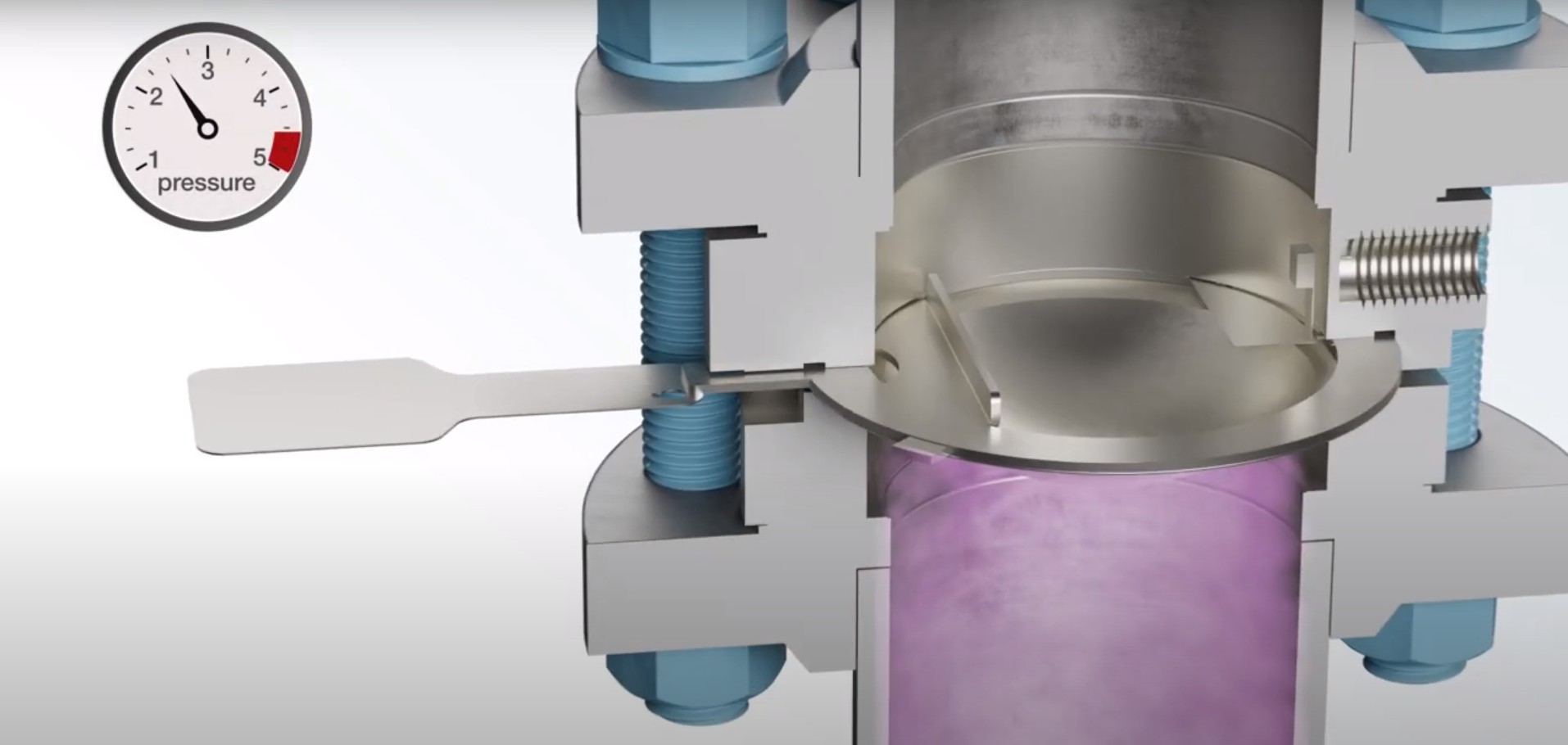
Why Choose Rupture Discs Over Other Pressure Relief Devices?
While devices like safety valves and air pressure relief valves are common, rupture discs offer unique advantages and features:
- Cost-effective solution.
- No moving parts, reducing the risk of mechanical failure.
- Quick response to overpressure scenarios.
Leading Rupture Disc Manufacturers and Suppliers
If you’re looking for rupture disc manufacturers or burst discs manufacturers, Ventil offers several reliable options. We are the best in reliable Rupture Disc Manufacturers in India Known for high-quality products that meet international safety standards. We are also leading Rupture Disc Suppliers in India, Providing a range of rupture disc types for diverse industries.
Conclusion
Rupture discs, or burst discs, are indispensable safety devices for high-pressure systems. Whether used in air compressors, pressure vessels, or steam systems, we provide reliable protection against overpressure scenarios.
Ventil boasts a trusted rupture disk manufacturers and rupture disc suppliers, offering solutions that adhere to international quality standards. By selecting the right rupture disc types for your specific needs, you can ensure the safety and efficiency of your industrial systems.