Flame arrestors are critical safety devices used in industries dealing with flammable gases, vapors, or liquids. These devices prevent flames from propagating through piping systems, storage tanks, or vent lines, thereby minimizing the risk of explosions. Selecting the right flame arrestor is essential to ensure optimal protection and compliance with industry regulations.
In this guide, we’ll explore the key factors to consider when choosing a flame arrestor, its types, applications, and how to ensure long-term reliability.
What is a Flame Arrestor?
A flame arrestor is a device that allows gases or vapors to pass through while extinguishing flames by absorbing heat and reducing the temperature below the ignition point. It consists of a metal mesh or a cellular structure that disrupts flame propagation, making it an essential component in explosion prevention systems.
Key Factors to Consider When Selecting a Flame Arrestor :
1. Type of Flame Arrestor (End-of-Line vs. In-Line)
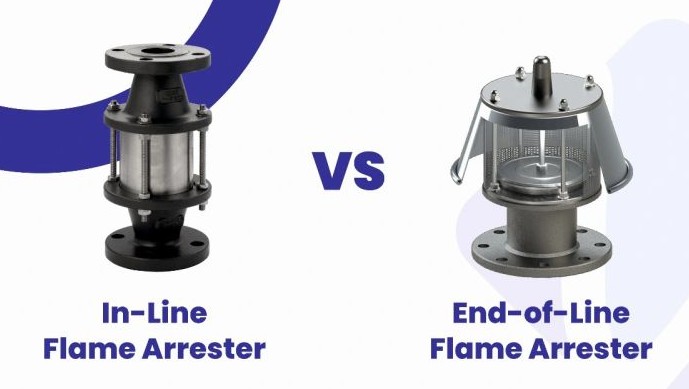
Flame arrestors are categorized based on their installation location:
- End-of-Line Flame Arrestors : Installed at the end of vent lines to prevent flames from entering tanks or vessels. Commonly used in storage tanks and vapor recovery systems.
- In-Line Flame Arrestors : Installed within piping systems to stop flame propagation in both directions. Used in process pipelines, fuel storage, and gas transportation.
2. Explosion Group & Gas Classification
Flame arrestors are designed for different explosion groups based on the gas they will be handling. The gas classification follows IEC 60079-20-1 and NFPA standards:
- Group IIA : Low-energy gases like propane
- Group IIB : Medium-energy gases like ethylene
- PGroup IIC : High-energy gases like hydrogen & acetylene
3. Operating Conditions (Pressure & Temperature)
Understanding process conditions is crucial for selecting a flame arrestor:
- Operating Pressure : Standard models handle atmospheric pressure, but specialized units can withstand high pressures.
- Operating Temperature : Ensure the flame arrestor material can withstand extreme temperatures, especially in high-heat environments.
4. Flow Rate & Pressure Drop
Selecting a flame arrestor with the right flow capacity ensures efficient operation:
- Higher flow rates : require larger flame arrestors to prevent excessive pressure drop.
- Too much pressure drop : can disrupt processes and reduce efficiency.
5. Bi-Directional or Uni-Directional Protection
- Uni-Directional Flame Arrestors : Protect against flame propagation in one direction only.
- Bi-Directional Flame Arrestors : Prevent flames from traveling in both directions, ideal for pipelines with bidirectional flow.
6. Compliance with Safety Standards
Ensure that the flame arrestor complies with industry safety regulations, such as:
- API 2000 - Venting Atmospheric & Low-Pressure Storage Tanks
- NFPA 69 - Explosion Prevention Systems
- ATEX 94/9/EC - European Explosion Protection Directive
- ISO 16852 - nternational Standard for Flame Arrestors
7. Material Selection for Corrosion Resistance
Flame arrestors are exposed to harsh industrial environments. The material should resist corrosion, temperature extremes, and chemical exposure.
Common materials used:
- Stainless Steel (SS 304/316) - Best for general industrial applications.
- Aluminum - Lightweight but limited corrosion resistance.
- Hastelloy & Inconel - Ideal for highly corrosive environments.
8. Maintenance & Cleaning Requirements
Over time, flame arrestors can accumulate debris, clogging the mesh and reducing effectiveness. Choose a model with:
- Removable elements for easy cleaning
- Self-cleaning features (optional)
- Access to maintenance without system shutdown
Choosing the Right Manufacturer & Supplier :
Not all flame arrestors are created equal. Partnering with a reputable manufacturer ensures product reliability. Look for:
✅Certified Manufacturers – Ensure compliance with global standards (API, NFPA, ATEX, ISO).
✅Custom Solutions – If your system has unique needs, work with manufacturers who provide tailored solutions.
✅Proven Track Record – Check reviews, case studies, and references before purchasing.
Conclusion
Selecting the right flame arrestor is crucial for safety and compliance. Consider type, gas classification, operating conditions, material, and standards before purchasing. Work with trusted manufacturers to ensure reliability.
💡 For high-quality flame arrestors designed for industrial safety, trust Ventil Team. Contact us today for expert guidance and reliable solutions. 🚀